Product Showcase
Precision Machinery, Intelligent Future – Hankun Intelligent delivers efficient and reliable industrial solutions for you.
Product Showcase
Fully Automatic Servo Tapping Machine
Polishing Machines
Feeding Machines
Dual-Spindle
Fully Enclosed
Tapping Machine
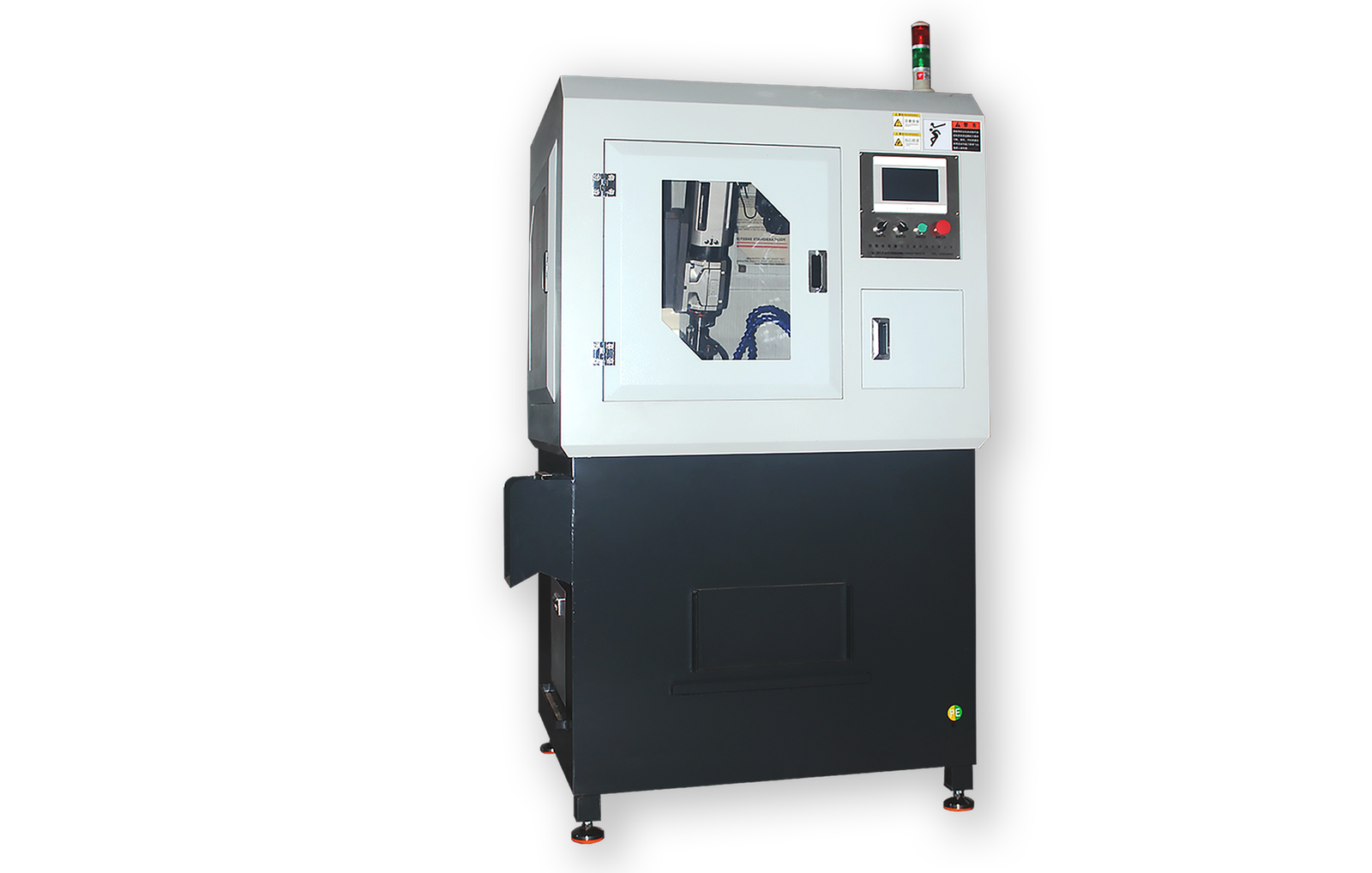
Hankun Intelligent Tapping Machine: Tapping, Reaming, Chamfering – All in One Step.
Hankun Intelligent’s high-efficiency tapping machines combine precision, speed, and versatility. Ideal for precision parts and complex workpieces, they boost productivity, meet diverse needs, and enhance your market edge.
Product Details
Intelligent and Efficient
The Driving Force
Tapping, Reaming, Chamfering
All in One Step
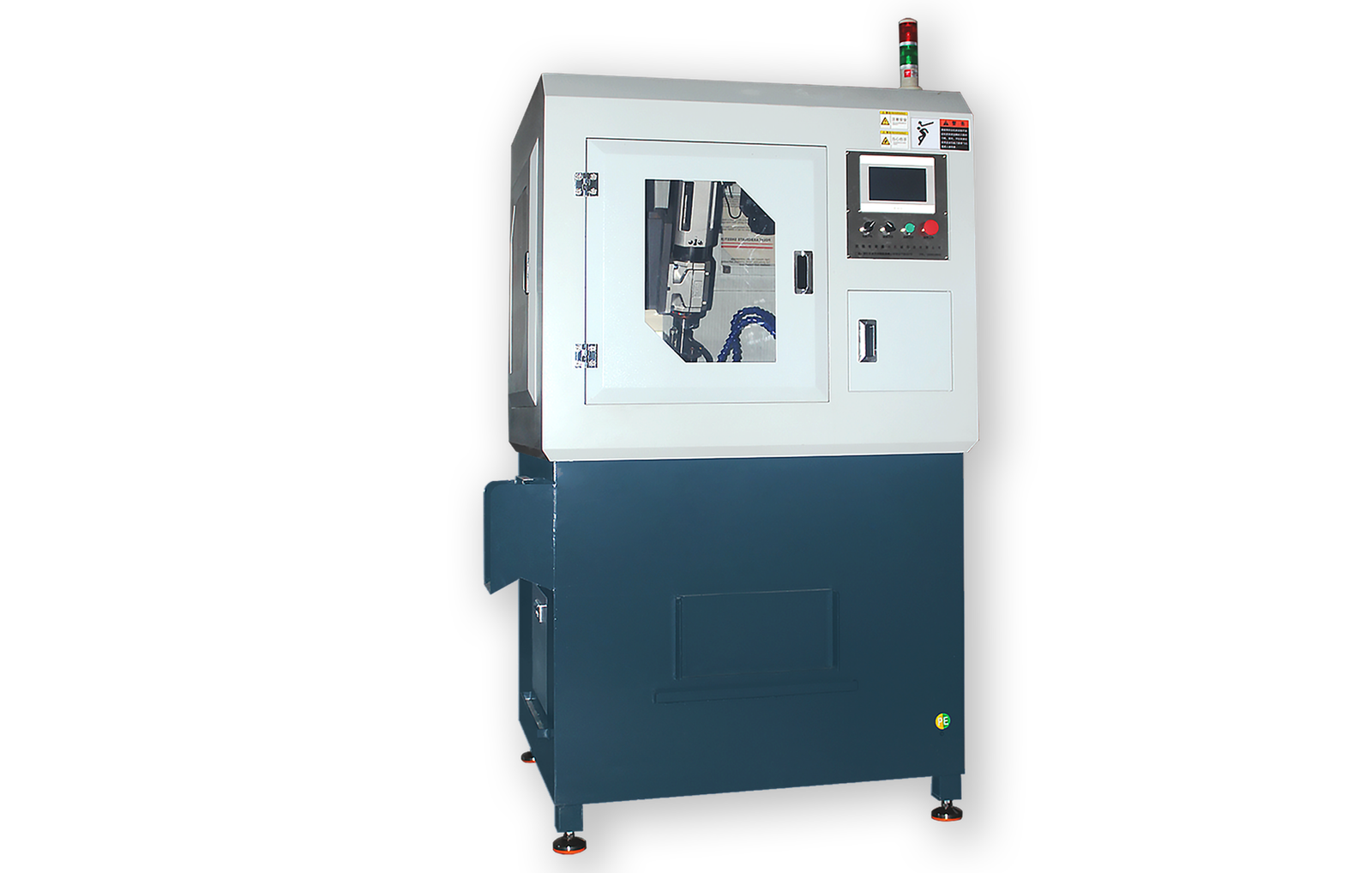
Dual Servo Ball Screw Power Head
Oversized Ball Screw and Spline
30% Performance Boost
Closed-Loop Servo Motor
Precision Positioning
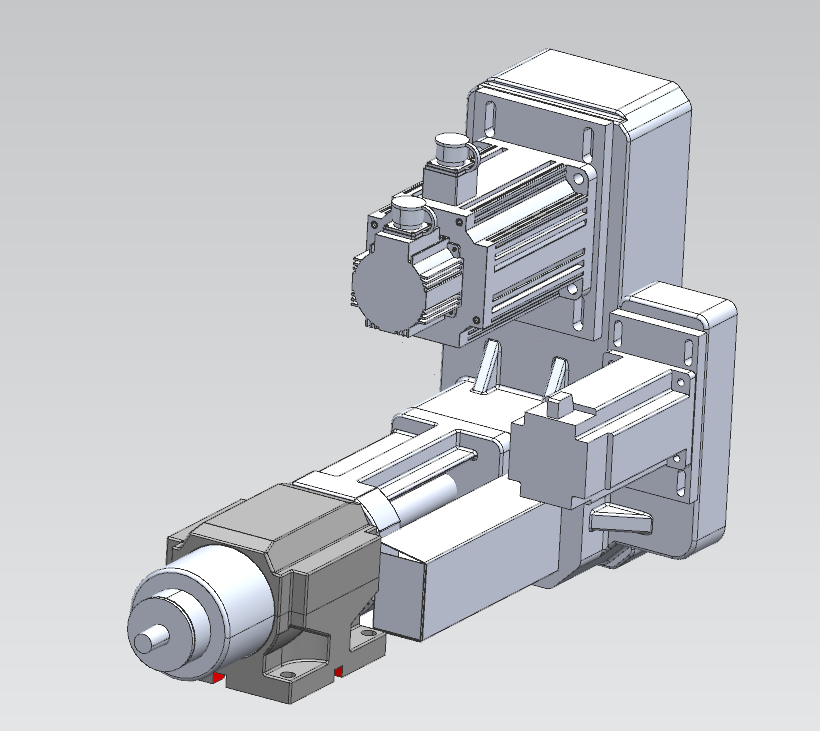
100% Made in China
Integrated Sand Casting Molding
Minimal Deformation, Exceptional Stability
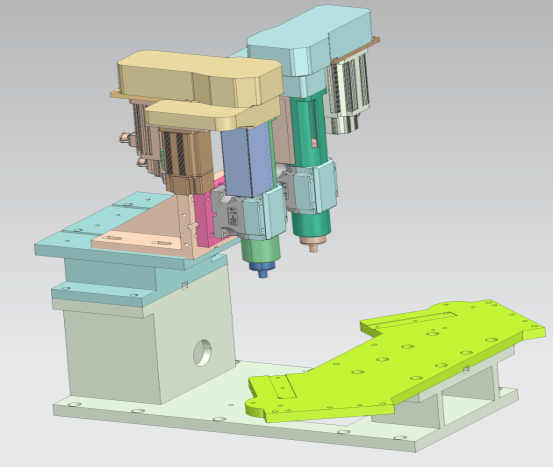
Hankun Intelligent Tapping Machines are designed for efficient and precise thread processing. Whether for precision parts or complex workpieces, our machines handle them with ease, significantly boosting your productivity and reducing operational costs. Choose Hankun Intelligent for flawless threads and a powerful boost to your manufacturing operations!
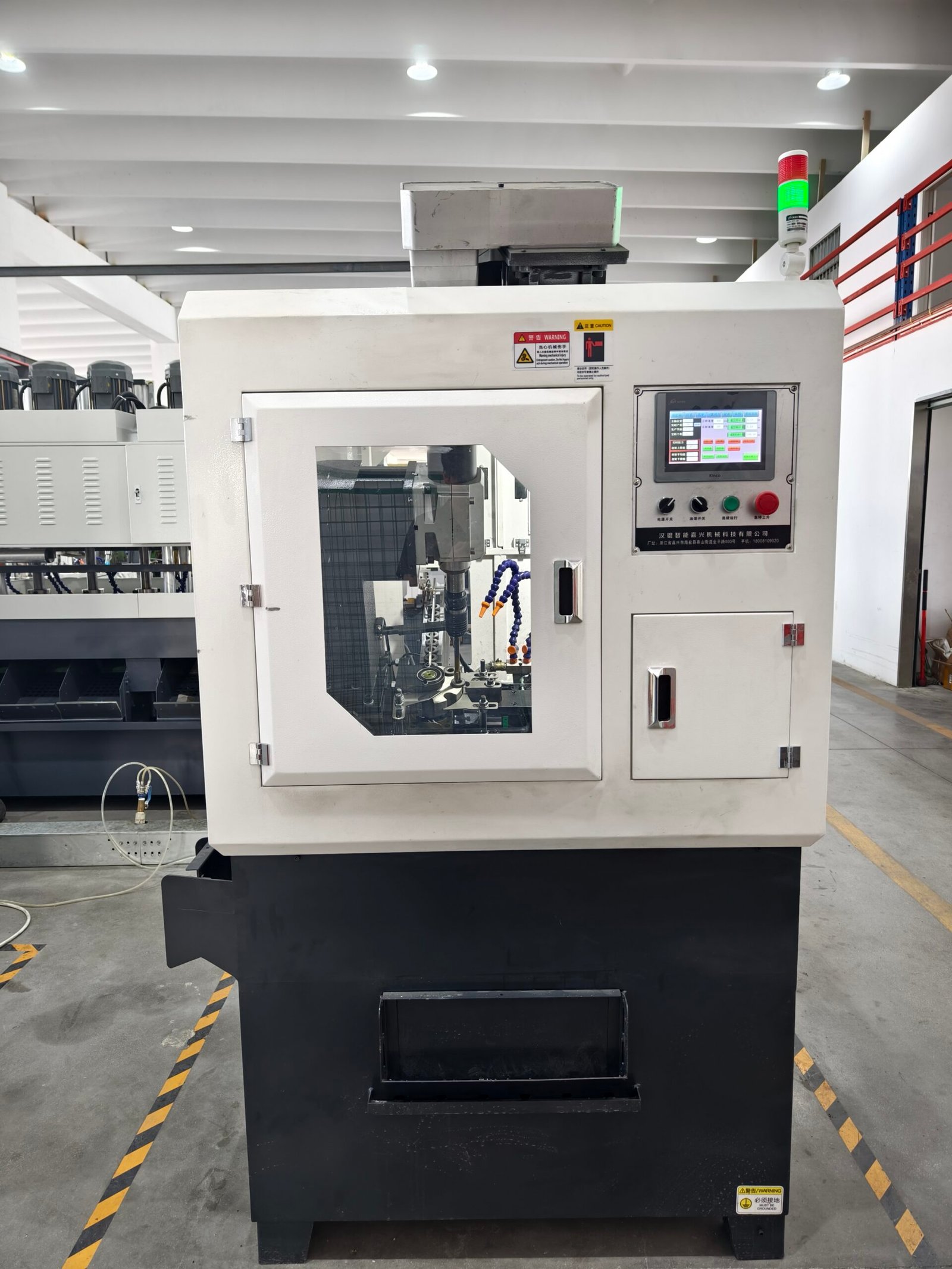
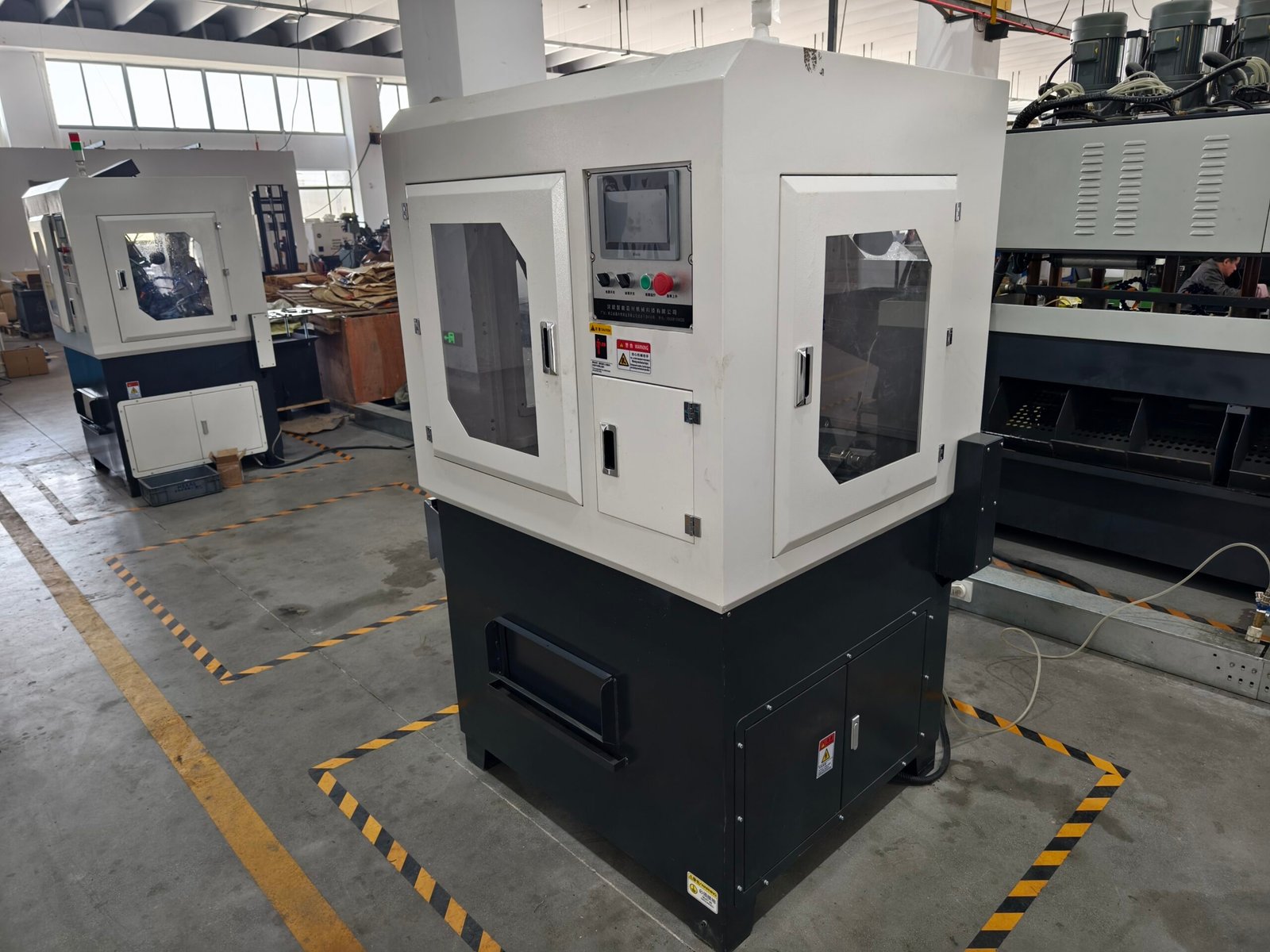
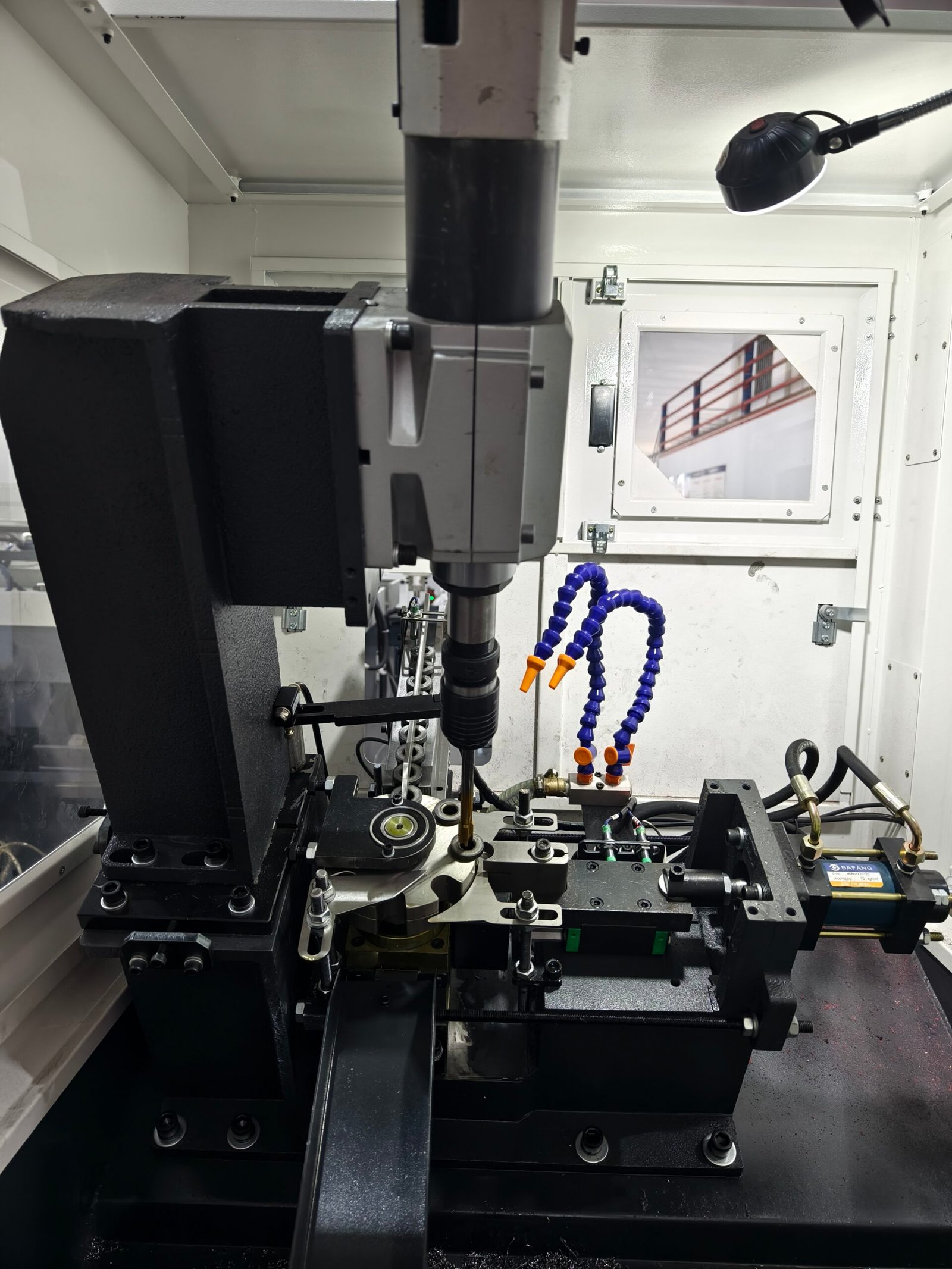
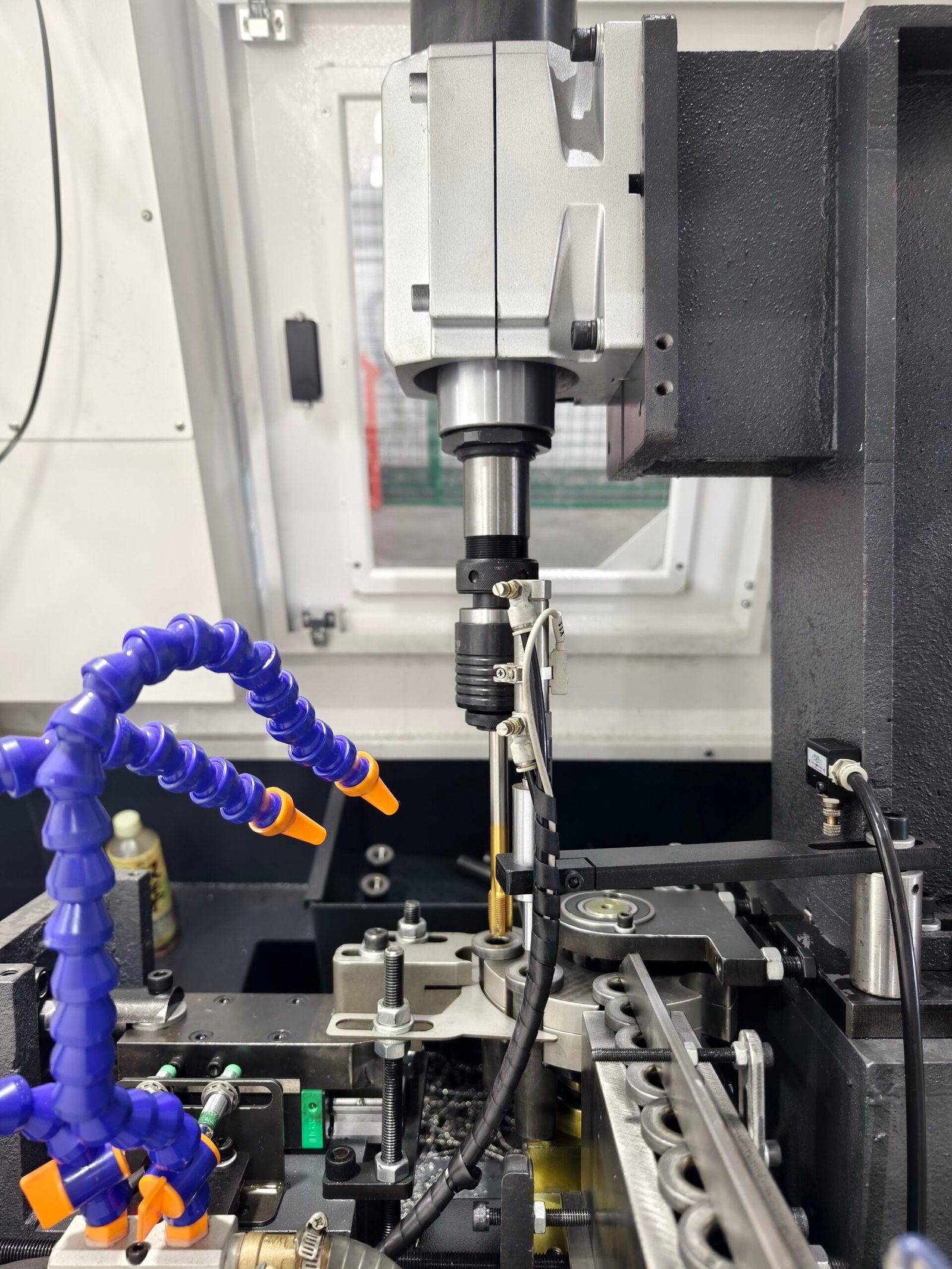
(Optional Push Plate Feeder or Vibratory Bowl Feeder)
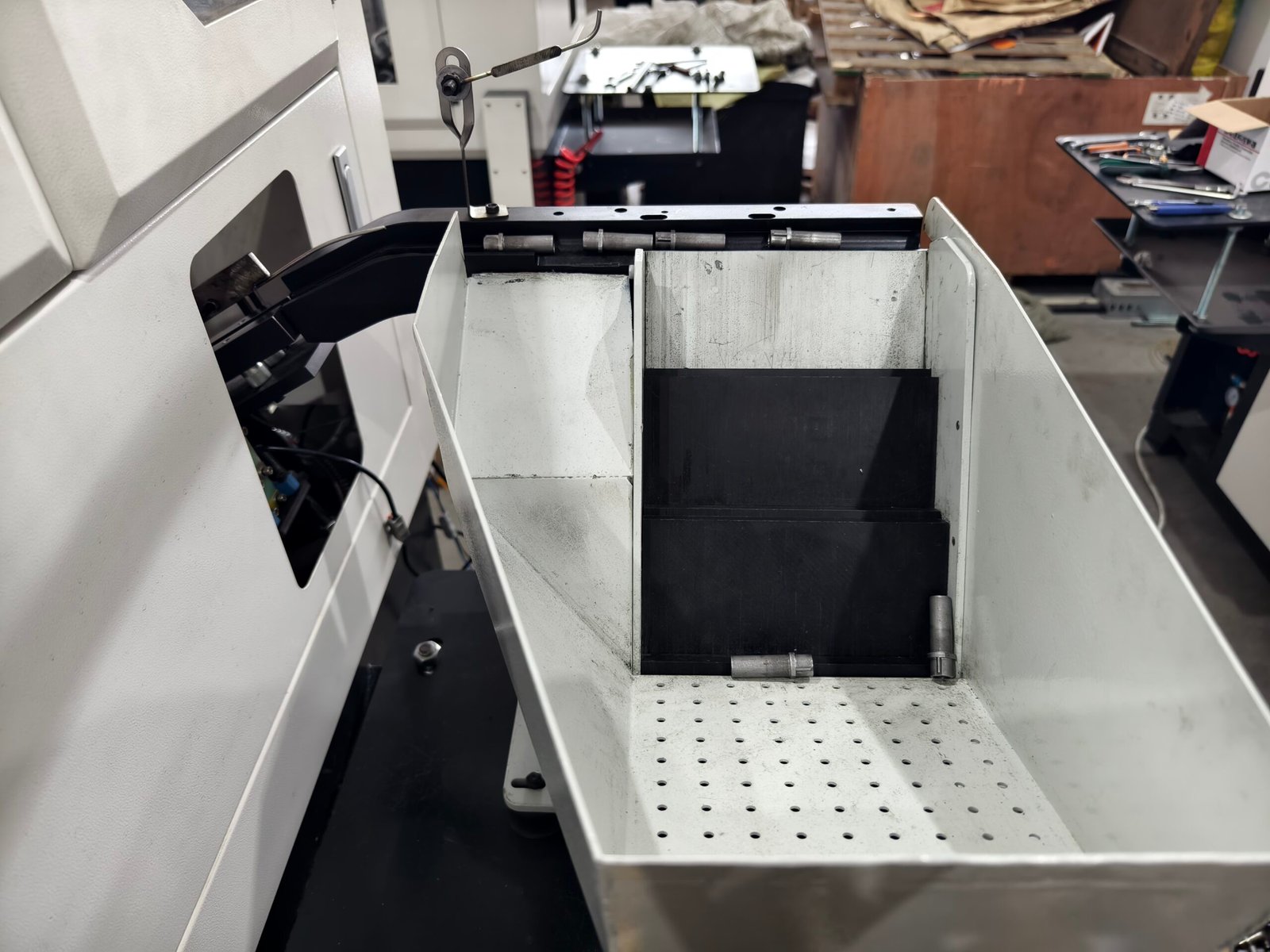
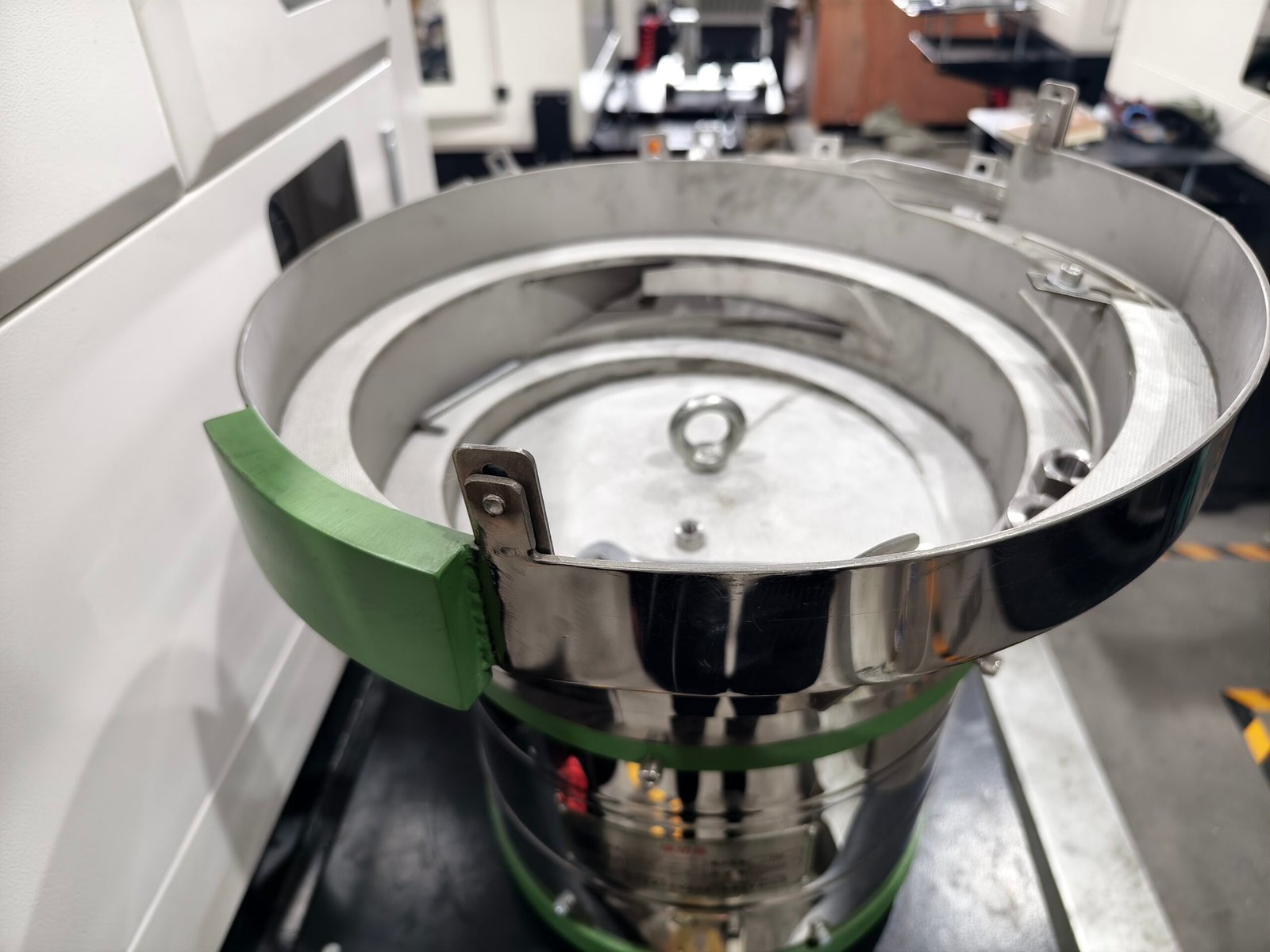
Plug-in 7-inch IoT Touchscreen: Scan the QR code to download the mobile control app, enabling remote data monitoring and equipment control.
Customizable Parameters: Adjust tapping speed, torque upper/lower limits for protection, and monitor real-time production efficiency and output for precise control.
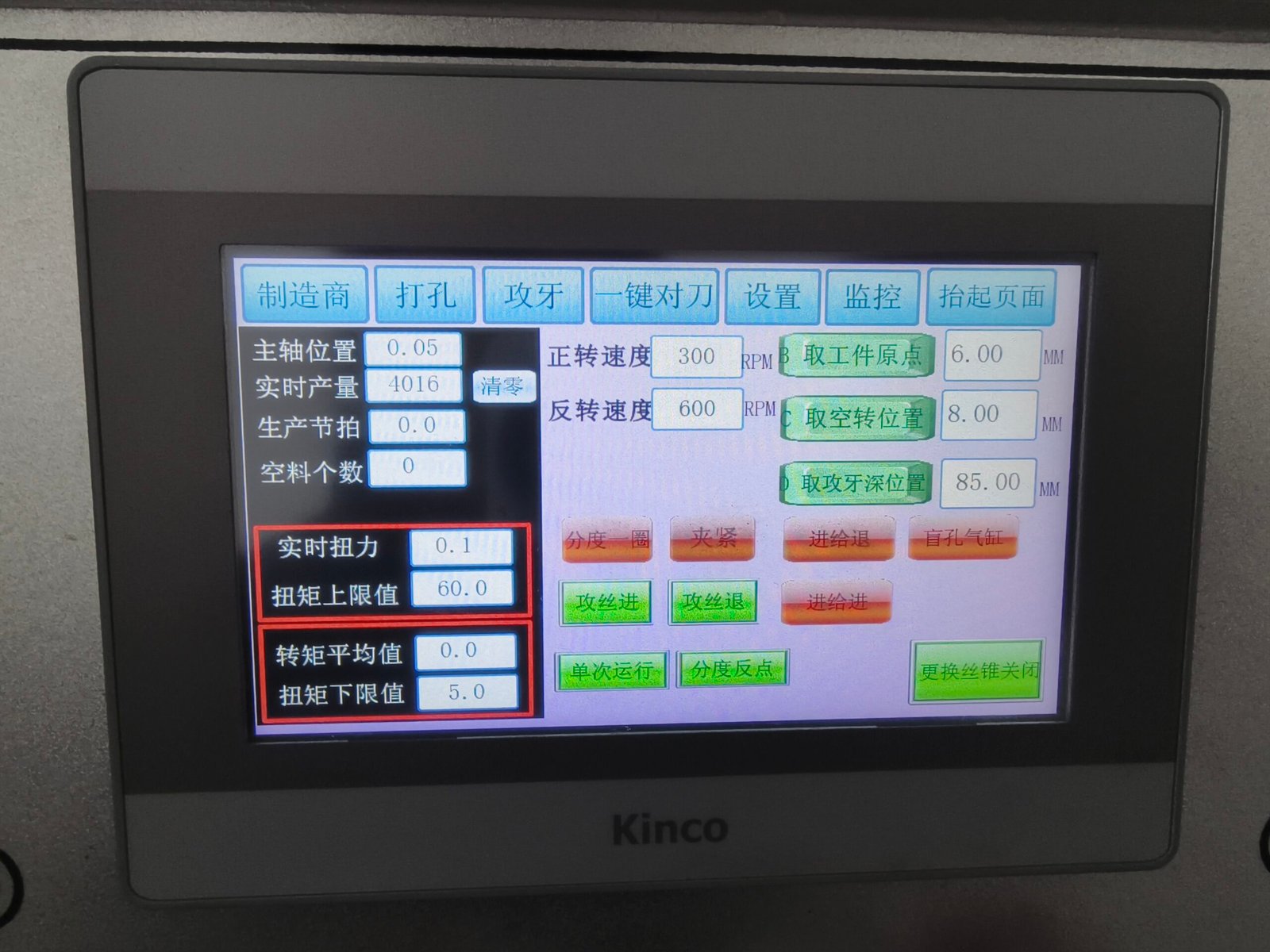
Efficient Tool Change: One-touch setup for switching product specs and tools, with adjustable safety distance and tapping depth for special products.
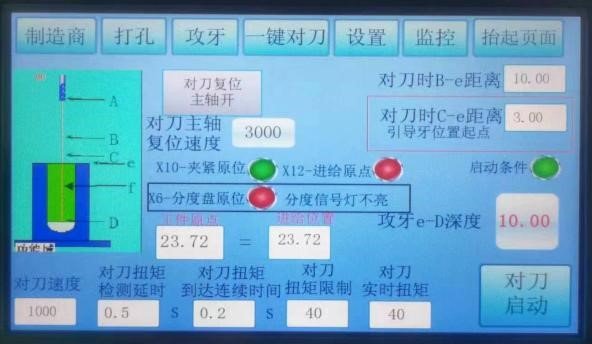
Versatile Threading: Set thread pitch, switch between forward/reverse threading, and enable quantity-based stop alarms with fine-tuned timing for each process.
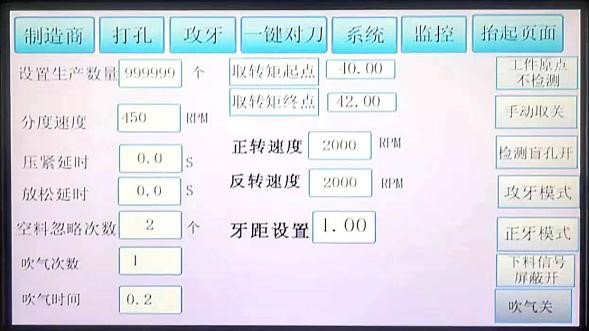
More Technical Specifications of Tapping Machine
Blind Hole Detection Mechanism (Right Diagram) Description: The mechanism employs a pneumatic cylinder telescoping device in conjunction with a proximity sensor. When a product’s blind hole is detected, the machine will halt operation and trigger an alarm. This design not only protects the tap but also prevents the production of defective parts.
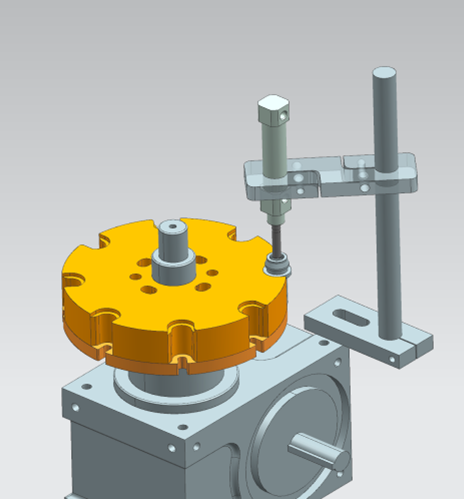
Discharge Chute and Tooling (Right Diagram) Description: Nuts are conveyed through the discharge chute, propelled by linear vibration and gravity feed into the tapping machine’s rotary tooling turret. The turret is equally divided into 8 stations, with each rotation advancing one station for a tapping operation, ensuring both machining accuracy and production efficiency.
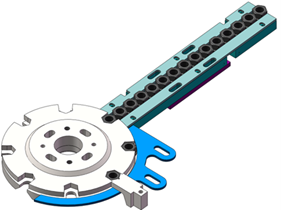
Indexing Mechanism (Right Diagram) Description: The indexing mechanism adopts an 8-station high-precision cam divider driven by a servo motor. The servo system is equipped with overload protection to safeguard the motor, divider, and associated components from damage during abnormal conditions, while maintaining high-precision cyclic indexing motion.
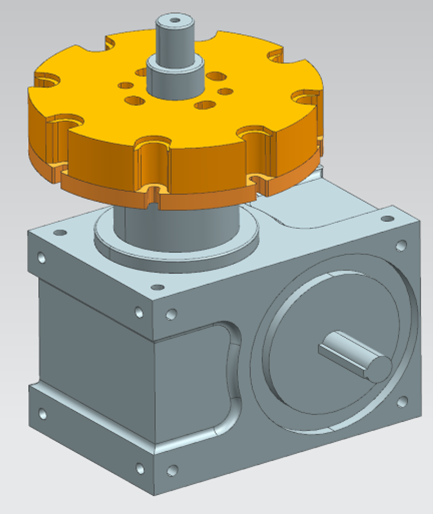
Clamping Mechanism (Right Diagram) Description: The pneumatic clamping system utilizes a cylinder-driven linear bearing slide table, coupled with a nut-matched product chuck to achieve high-speed and stable clamping operation. (Hydraulic clamping can be optionally configured based on actual product torque requirements.)
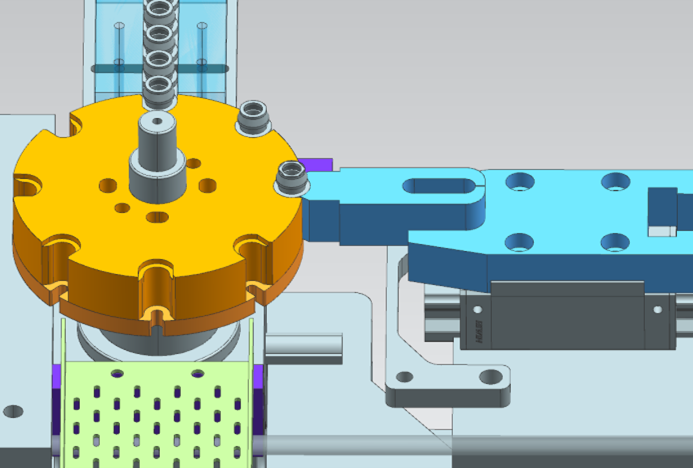
Power Head (Right Diagram) Description: The power head features a dual-servo ballscrew drive system with reinforced screws and splines, achieving 30% higher stability and durability than standard market offerings. Both the spindle motor and feed motor incorporate closed-loop servo control, guaranteeing superior repeat positioning accuracy. This configuration significantly improves thread quality while extending tap tool life.
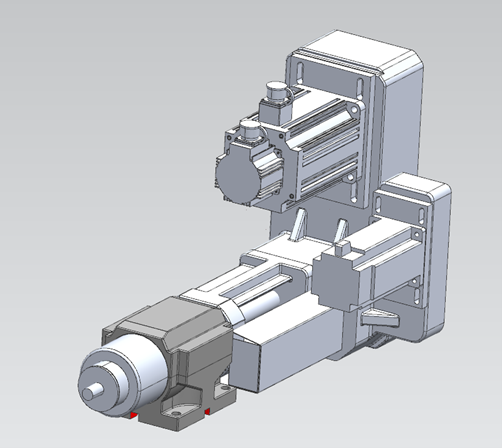
Machine Main Body (Right Diagram) Description: The machine’s primary structure utilizes a monolithic high-density sand-casting component, effectively enhancing machine rigidity while minimizing deformation. This integrated casting design provides superior stability and eliminates cumulative machining/assembly errors from multiple component fittings. The result is significantly improved machine positioning accuracy, ensuring consistent product machining quality and precision.
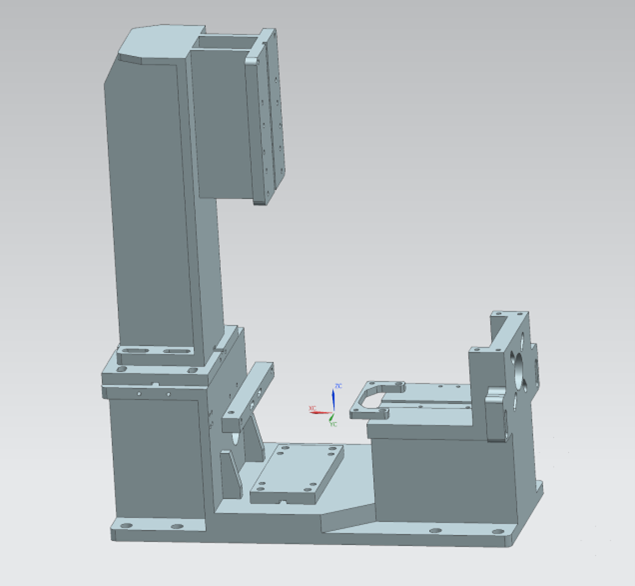
9 Core Advantages for Enhanced Production:
- IoT Integration: Remote control module for program upload/download, improving after-sales efficiency.
- Full Servo Drive: Real-time process data monitoring for error prevention and higher product yield.
- Smart Tool Change: One-touch setup for quick product and tool switching, boosting efficiency.
- Multi-Function Capability: Seamless switching between drilling, chamfering, reaming, and tapping, maximizing equipment value.
- High Compatibility: Rapid product changeovers and universal machine adaptability, increasing utilization.
- Enclosed Design: Noise reduction for a cleaner, quieter, and more professional workshop environment.
- Compact Structure: Space-saving design with optimized ergonomics and ample machining space.
- User-Friendly OS: Intuitive interface for quick operator training and multi-machine control, addressing labor challenges.
- High-Rigidity Construction: Solid cast iron body for superior stability, durability, and long-term performance
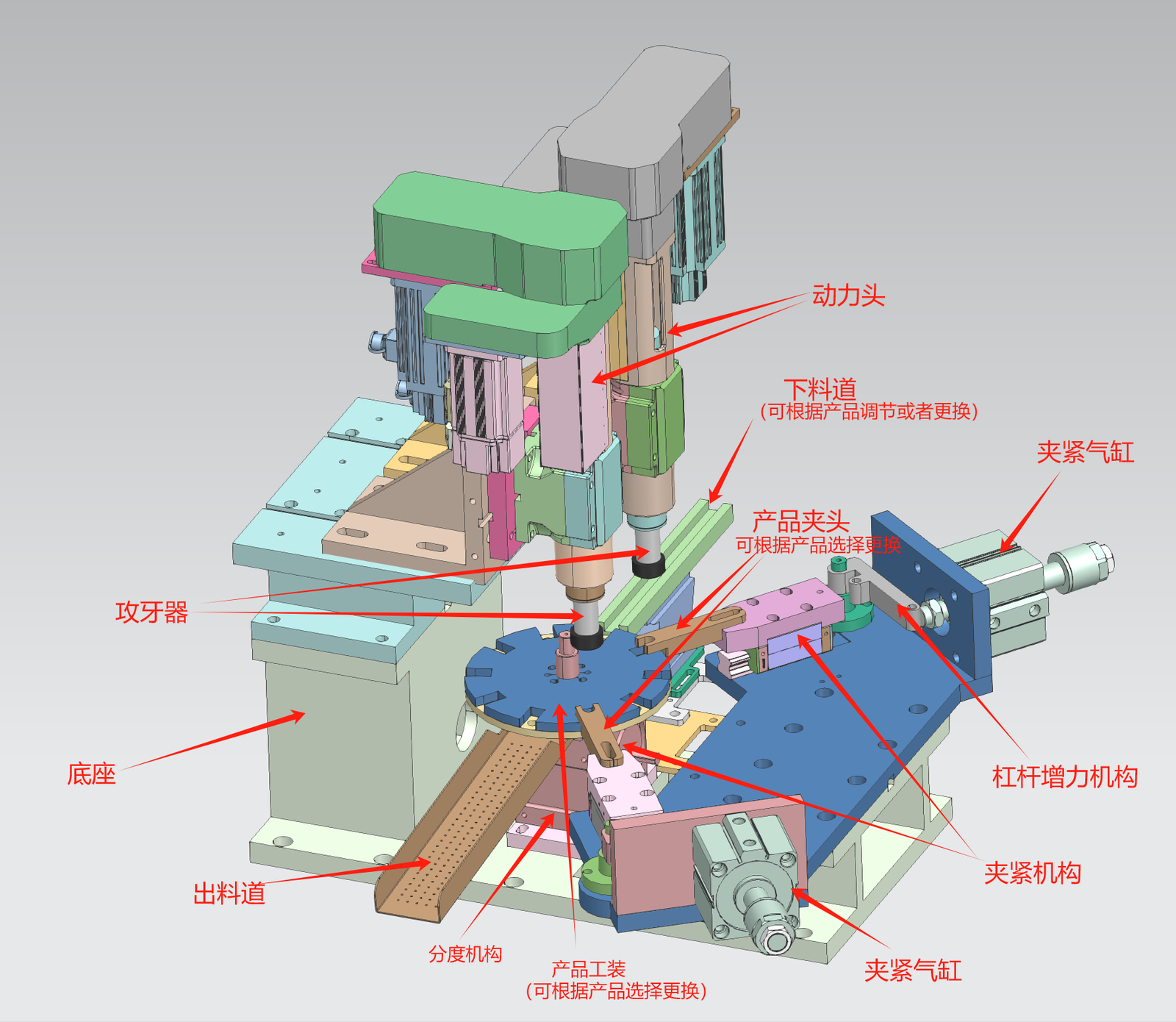
Technical Specifications of Han Kun Machine
- Tapping Range: M48-M52
- Axis Count: 1 axis
- Air Pressure: 0.5-0.6 MPa
- Tapping Speed: 1-120 RPM
- Production Efficiency: 1-2 pieces/minute
- Oil Tank Capacity: 60L
- Dimensions (L x W x H): 1400 x 1500 x 2200 mm
- Total Power: Approx. 10 KW
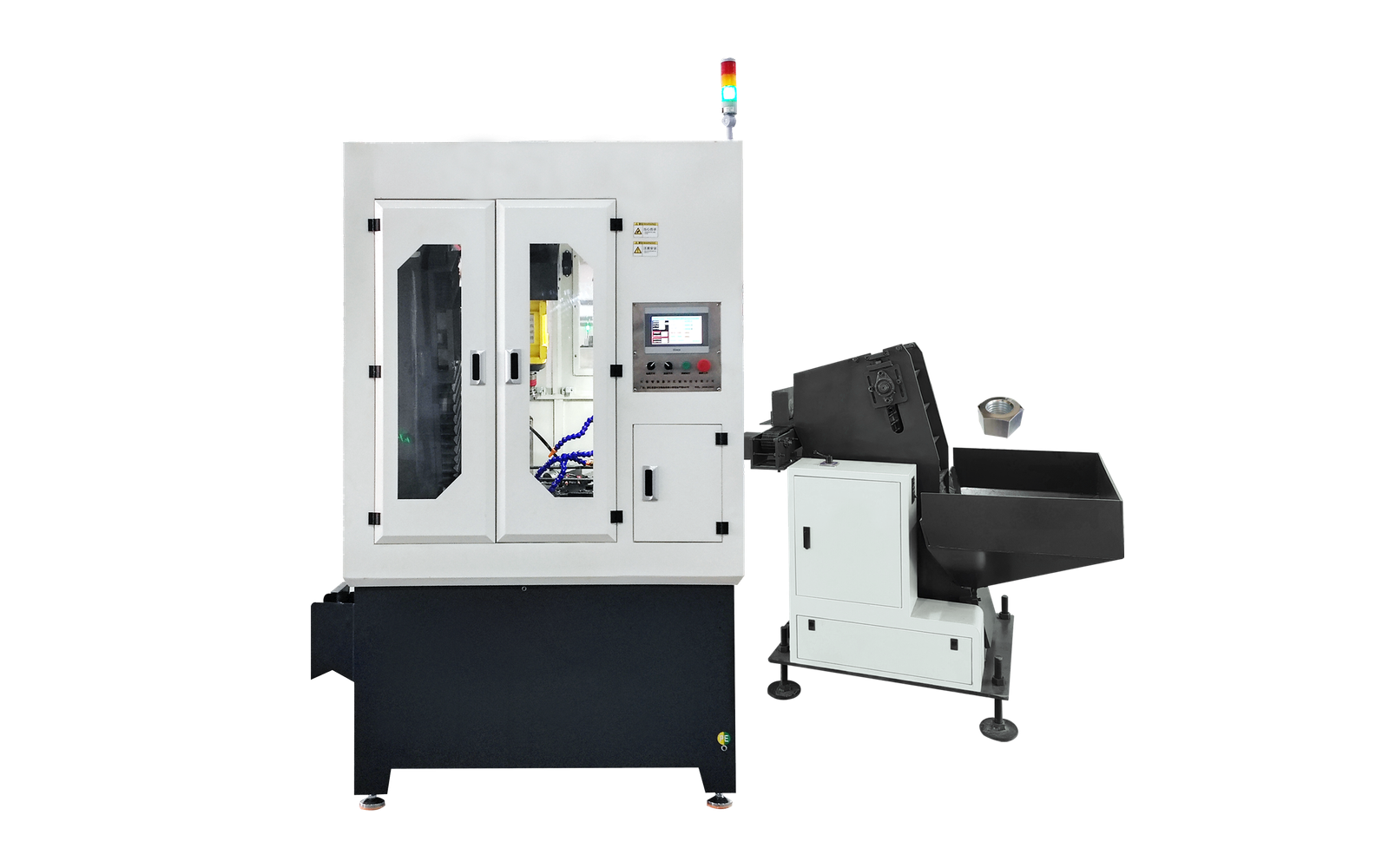
More Models Available